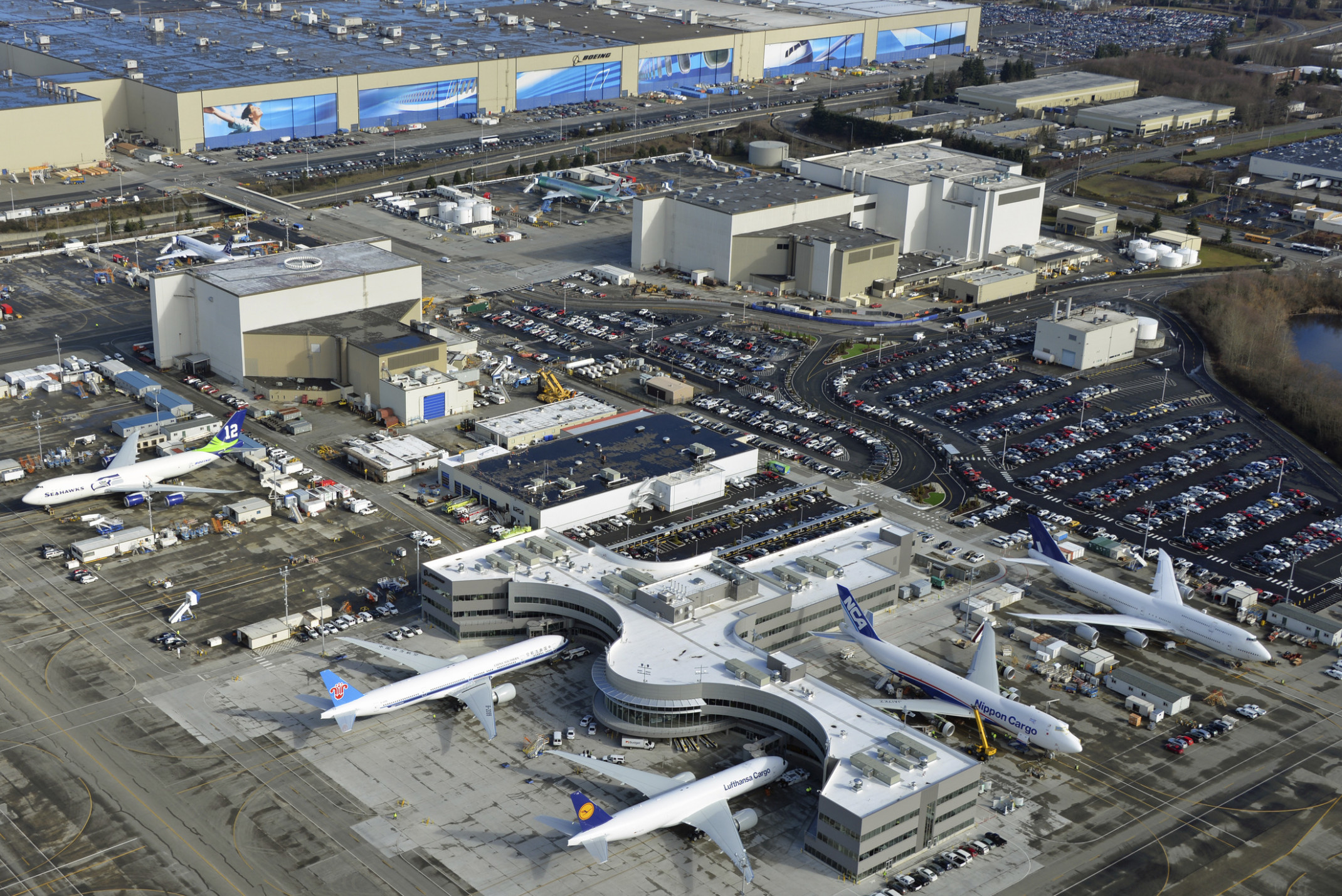
Project Location
Seven U.S. States
Services
Planning, architecture, interiors, engineering, strategy
Highlight
Boeing’s first LEED Gold project
Area
3,000,000 SF + across more than 500 projects
Projects
Programming, planning, and design not only meet the facilities’ wide range of needs, but also include solutions that respect the perspectives of international customers from diverse cultures and backgrounds.
Everett + Seattle
Boeing’s Delivery Centers are some of the most unique buildings in the world, mixing functional and cultural factors into a showroom for large-body commercial airplanes. Delivery Centers are classified and built as international airports with flight and logistic centers, but they also house both Boeing staff and their customer airlines in Class-A office space for months at a time as they carry out final negotiations, and they celebrate airplane delivery ceremonies in dramatic event centers. Across the design of three Boeing Delivery Centers, we’ve honed an approach where the entire center caters to customers’ experience of the Boeing brand: showcasing the planes on the tarmac outside. Sight lines, forms and shapes, transparency, lighting, and processional circulation enable ongoing visual connection to the aircraft from all levels. The seamless customer experience is backed by myriad behind-the-scenes technical design decisions, including revised vehicular traffic, airplane delivery stalls with essential service connections, “back of house” spaces including catering kitchens, and coordination with numerous governmental and private entities, including the TSA.
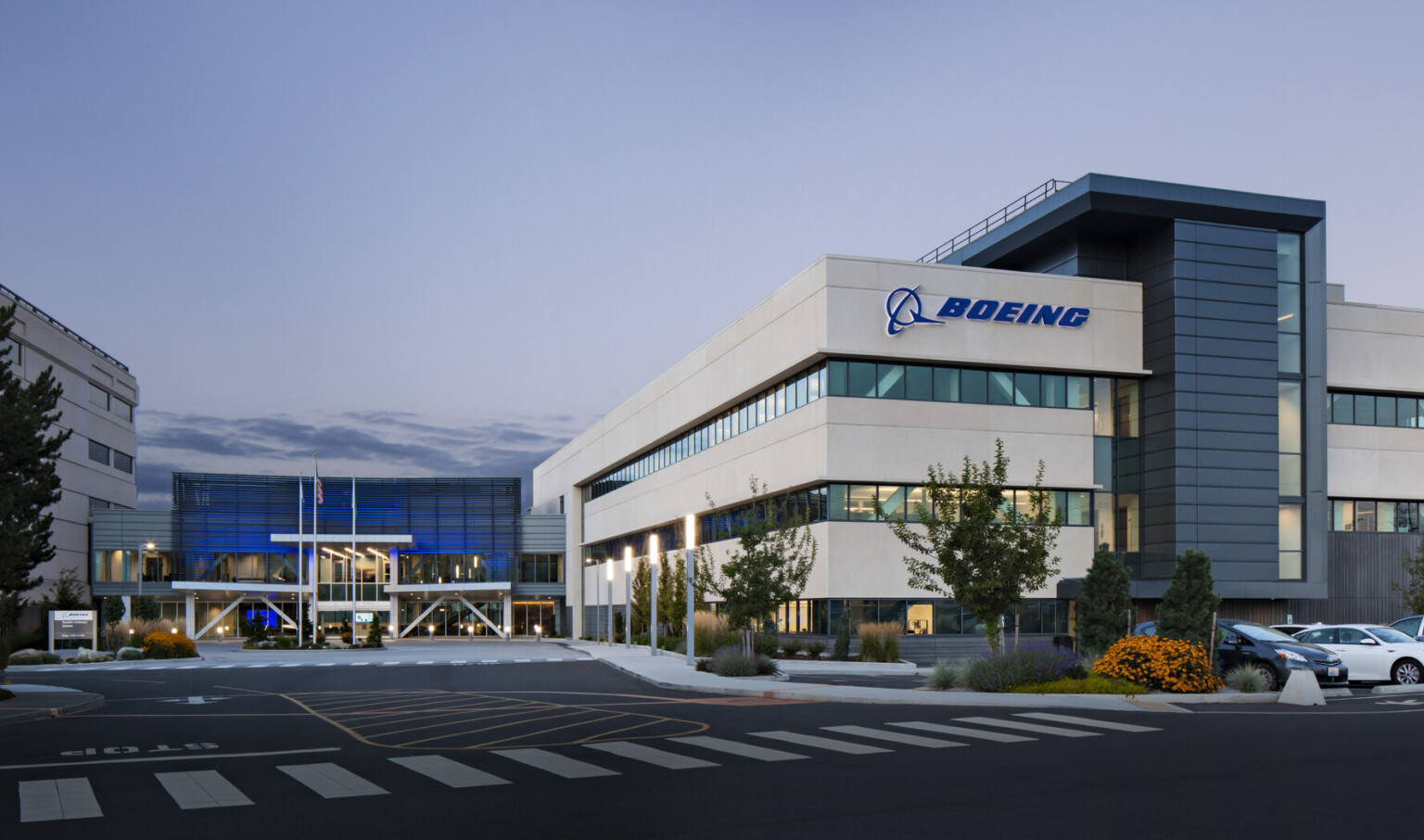
Boeing Seattle Delivery Center
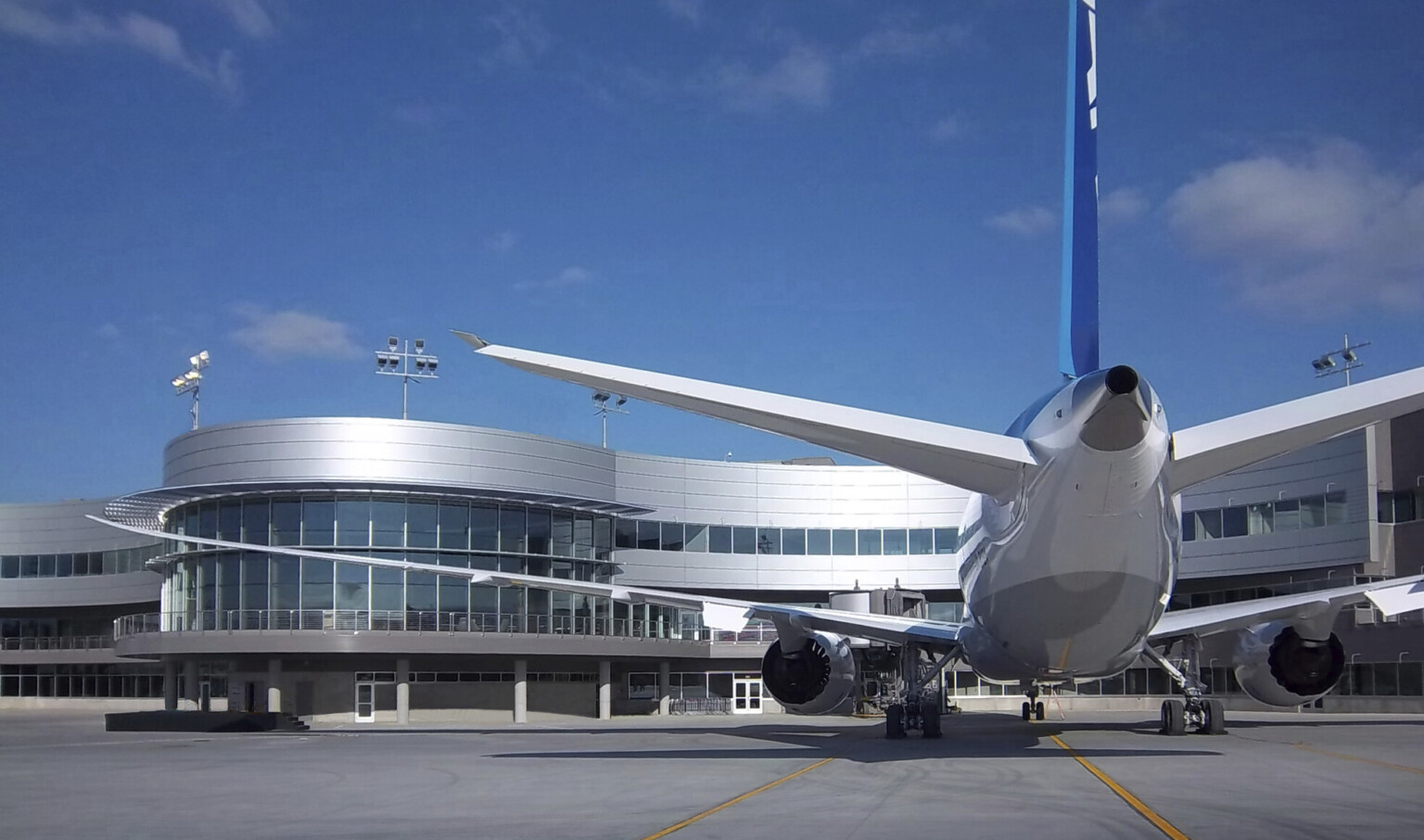
Boeing Everett Delivery Center
Update Rollout
As Boeing implemented new Global Design Standards – informed by DLR Group’s research into the connection between indoor environmental quality and employee satisfaction and performance – they identified multiple rollout sites where workplaces would become lighter, brighter, and denser, as well as host more meeting space. With hundreds of internal services employees relocating from the Seattle area to Boeing’s Mesa, Arizona campus, testing the new standards became a key factor in retention. Improved natural light and transparency, a greater quantity and diversity of meeting spaces, and the introduction of a popular new space type: knowledge cafes as places to eat and work improve the employee experience. Both floorplates previously held a sea of high-walled cubicles. While the size of individual workstations was brought down, additional meeting spaces and central knowledge cafés are now available. Four neighborhoods loosely based on employee function help break up the office space and provide wayfinding and branding opportunities. The projects were phased, with tight timelines and budgets. Existing ceilings and a maximum of existing walls were kept to conserve the budget and shorten the timeline. The second phase allowed updated ceiling and lighting in addition to updated workstations and meeting spaces. Working with Boeing’s facilities and maintenance department, we evaluated and tested the cost and glare performance of multiple lighting systems. Our electrical engineers leveraged the fluorescent to LED conversion to not only reduce operating costs, but also to improve employee health and comfort. The solution virtually eliminated glare complaints, a previously time-intensive maintenance ticket pattern.
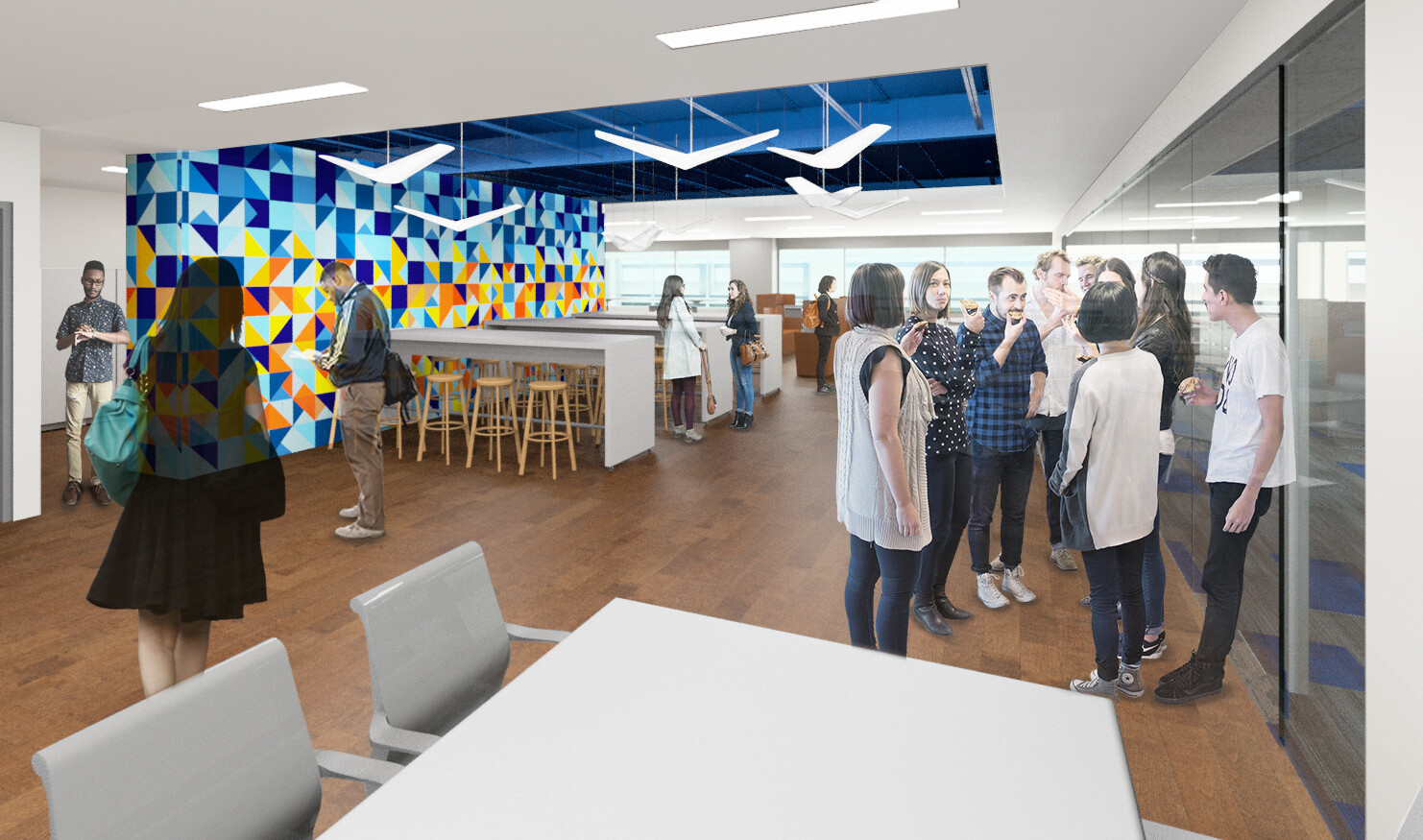