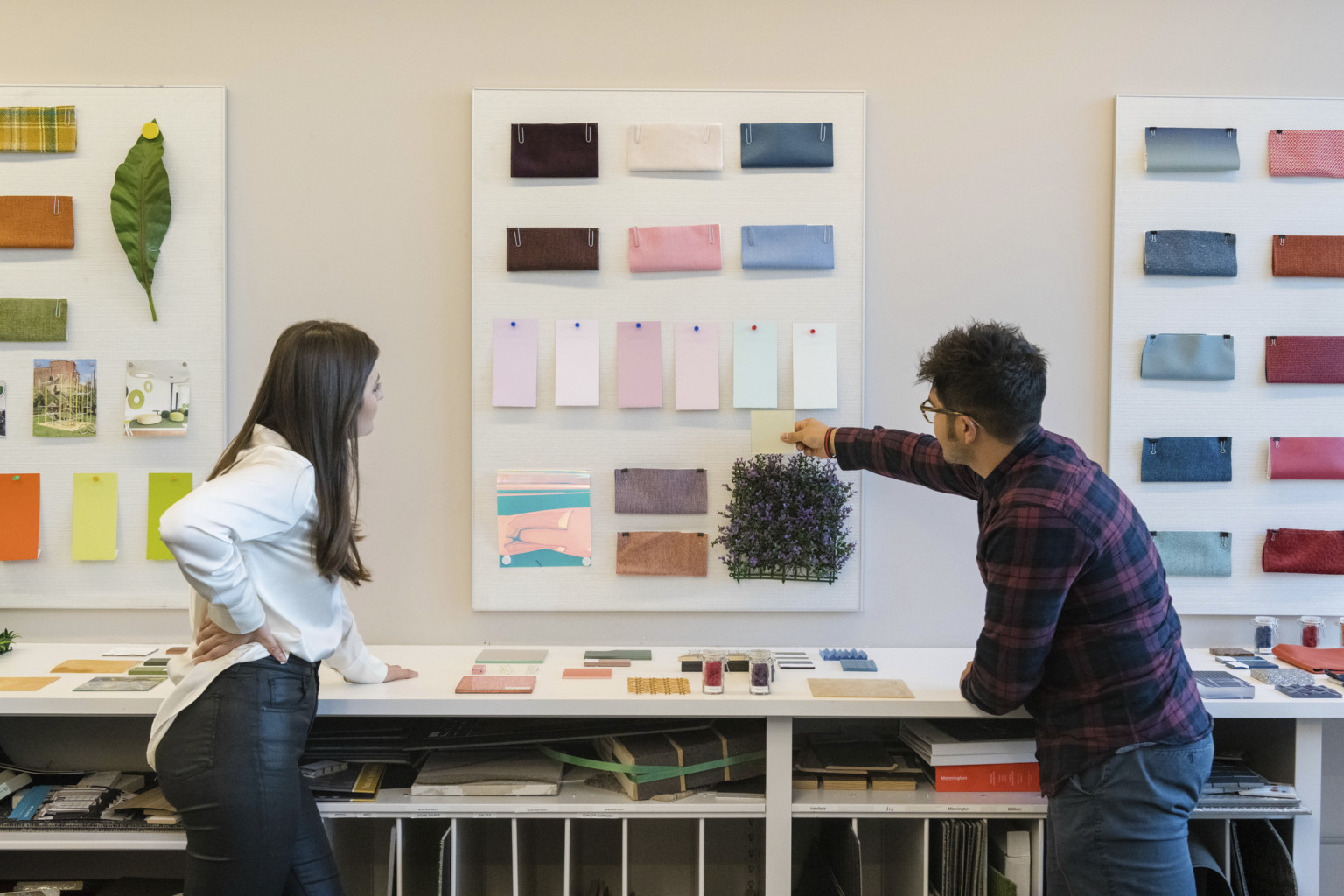
Materials Transparency in Use: Addressing Gaps
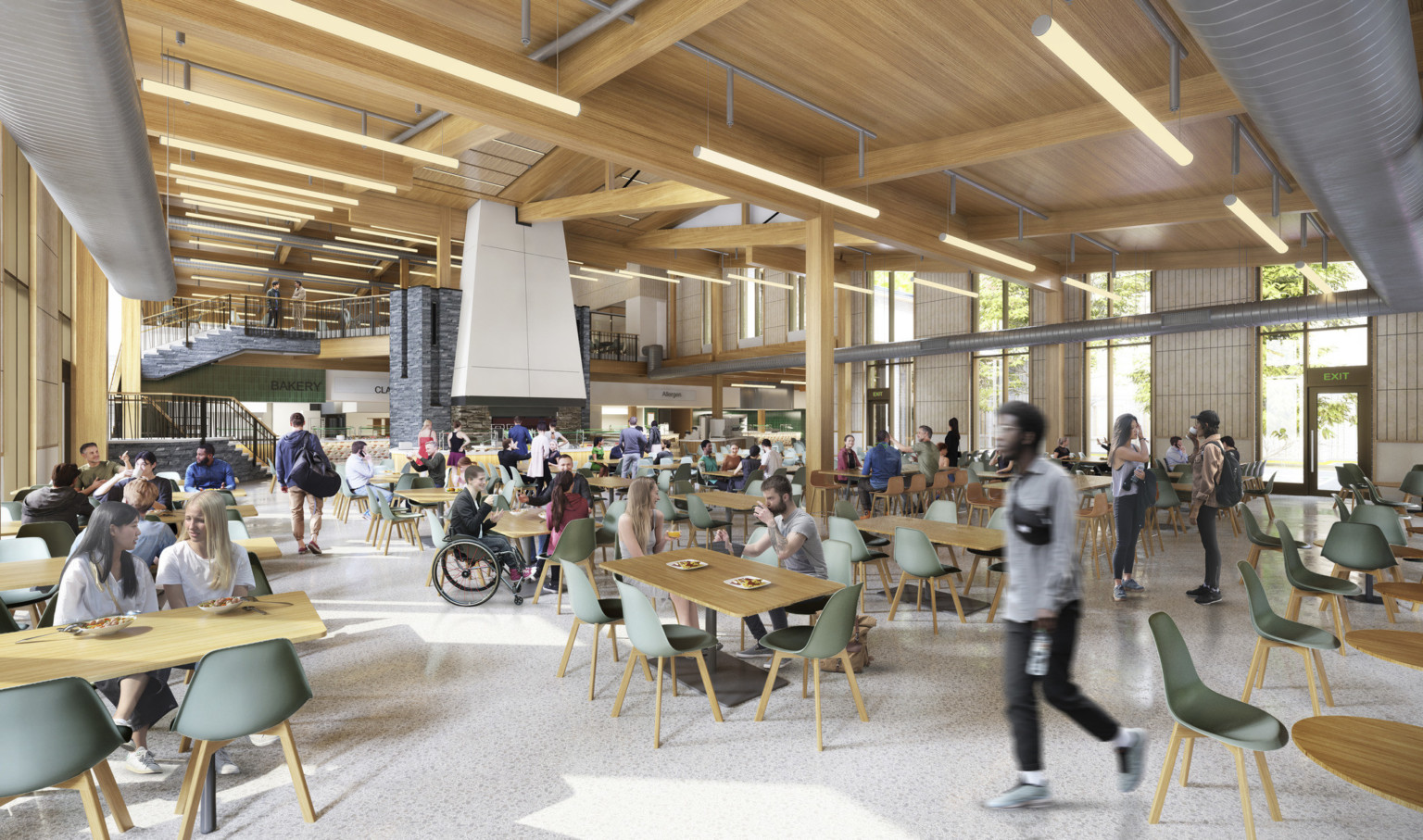
In the last five years, and with several Materials Petal equivalency/full pursuits underway in our project portfolio, we’ve observed a range of a 30% decrease to a 53% increase across various material certifications. The variance in participation applies to both well-represented and emerging participating divisions alike – hello, Construction Specifications Institute – which is both exciting and surprising. The observed decrease is evidence of something many of our design team members do not anticipate when starting their project’s vetting; decertification and/or allowing certifications to lapse after their expiration date. Decertification has become a major barrier for more design teams acknowledging materials achievements in the way we currently vet aesthetics, cost, and durability.
Firms need tools with open APIs across all certifying bodies to navigate this complexity. Firms also need designers who understand and appreciate we’re still in the sweat equity phase of verified materials transparency. These two items could yield increased consistency in green building certification and reviewer protocols, among other pros. Perhaps continuing to celebrate how far the industry has come is one path forward to continue the momentum. Addressing observed gaps is also another.
Here are a few areas where our industry could be solicitous:
- Adhesives and sealants: We need both volatile organic compound emissions and content confirmation, especially when it comes to structural joints or epoxy anchors. We typically must vet two or three manufacturers before we find a solution with confirmed use on a similar project and satisfactory confirmation – keep in mind certifications are left to expire, so we have to exercise the process anew for each client. Similarly, adhesives or sealants that are part of a warrantied assembly where only the tangible finish layer has achieved a Red List Free Declare label, or something similar, has become a pattern. We often get excited about a product and then pivot away from specifying because parts of the compatible assembly don’t have the same level of transparency.
- Domestically sourced tile: There are a few exceptions but certified product from small- to mid-sized manufacturers is hard-to-find. This difference in resources, especially in the case of this product type, causes designers to weigh trade-offs between verified achievement versus celebrating local materials.
- Gypsum: For wall assemblies with the weight of today’s emphasis on optimized acoustics, in tandem with materials achievement, we are decently limited as prioritization in performance criteria is continuously revisited.
- Ancillary furniture and lighting: There are many aspects in these product categories where the sustainability story is still catching up to where the flooring industry was 10 years ago. On a recent project where RoHS – aka Restriction of Hazardous Substances – verification was required for lighting, of the 74 manufacturers engaged, 24 had not heard of this standard driving optimization in lighting.
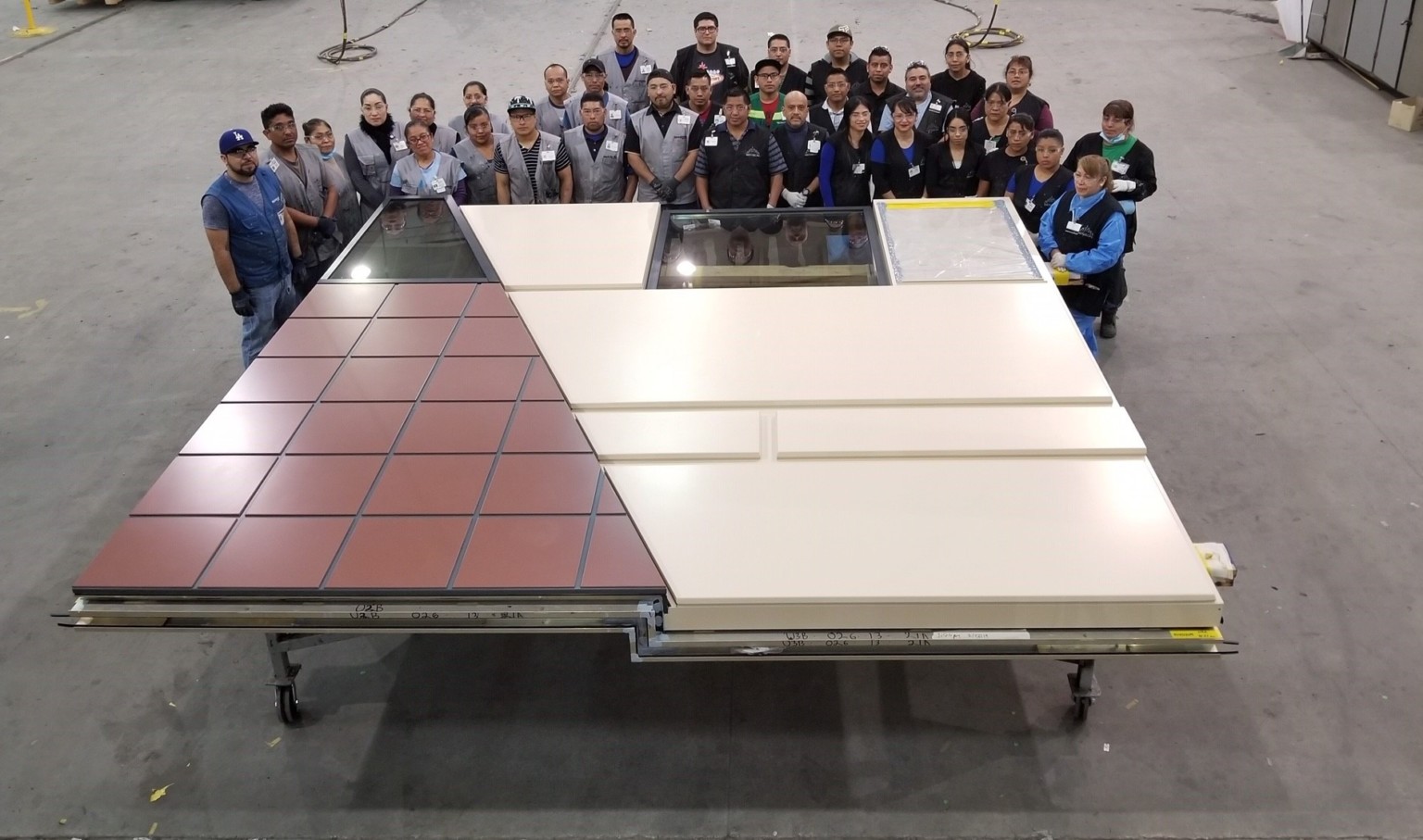
As a multi-disciplinary, integrated design firm, there are a multitude of challenges and opportunities to sole-sourced materials for a project. Among them, the speed of delivering modern technologies in the world we find ourselves in since early 2020 simply outpaces the speed of certification. Solving the gaps noted above takes persistence, and clients who trust their design teams to push on their behalf. We do need to celebrate those partnerships and accomplishments. Today, we have availability in steel studs, fully compatible resilient flooring assemblies, demountable wall systems, acoustic panels, textiles, raised access flooring, high performance coatings, and more ceiling tile options now available for peers and other building sectors to specify. Note, these are products both tangible and intangible.
Some product optimizations take truly less than 10 minutes. Vetting for energy code or confirmed durability might take longer than ingredients, carbon, or emissions verification, in some instances. But there is still not a holistic, automated easy button tying together all vetting factors designers must hurdle. While we work together to solve for the easy button, calling out these gaps might inspire more across our industry to meet the demand in anticipation of the ask, should it not have landed already.
Read how addressing these gaps led to an award winning innovation.
Sustainability Action Plan
Material transparency is just one of the ways we work to make a difference. To hold ourselves accountable to the best possible outcomes of our design choices, we’ve committed to industry initiatives and a sustainability action plan.
Click to download and view